About us
Our “Customer Driven Logistics”™ principle means your needs as a customer are our primary focus.
Since its founding in 1958, Lansdale Warehouse has furnished comprehensive logistics services in a public and contract environment for both national and international customers who require access to the United States markets.
key features
What we offer
Lansdale Warehouse is your partner in all aspects of supply chain logistics.
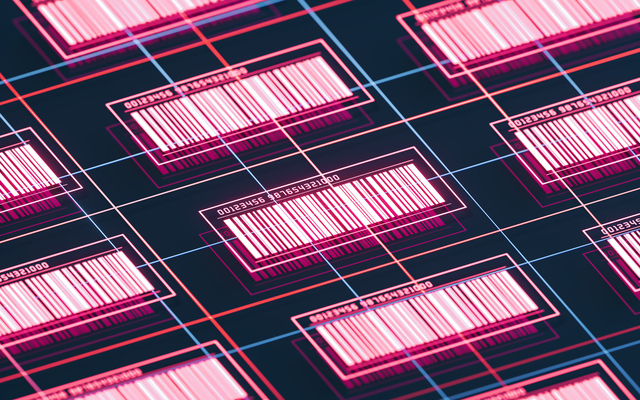
Intelligent Warehousing
Our advanced warehousing systems offer real-time inventory control, providing accurate, up-to-date information on inventory levels. Learn more…
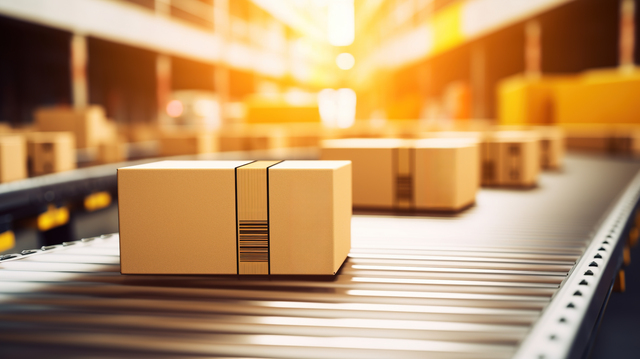
Fulfillment
We streamline the order fulfillment process, ensuring your products are picked, packed, and shipped to customers quickly and efficiently. Learn more…
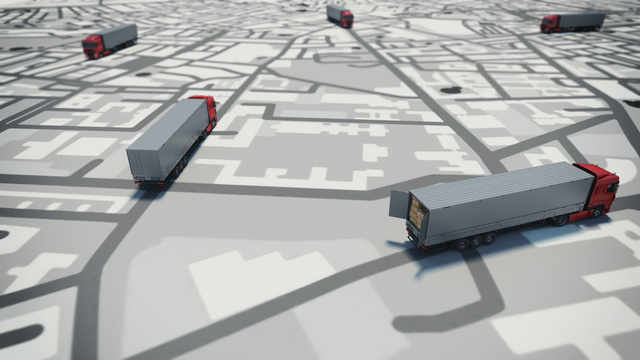
Local Delivery
Our experienced drivers ensure your products are delivered safely and on time, providing a convenient and reliable delivery solution for our customers. Learn more…
Service Excellence
We bring years of experience to the table. Growing from a traditional 3PL warehouse and storage company, we offer a complete complement of services to satisfy customer needs for the “last mile.”
Tailored Consultations
Personalized consultations that address your unique requirements, providing strategic insights and solutions is what we mean by Customer Driven Logistics.
Customer Support
Our dedicated and responsive customer support is always here for you.
Experienced and Flexible
As one of the longest-operating 3PL companies in the Mid-Atlantic region, we continue to adapt to changing market conditions to solve customers’ warehousing, fulfillment, and shipping needs.
What are you waiting for?
Ready to take the next step? Explore our services and get in touch today for a consultation. Together, we’ll make it happen.
Latest news
News and information from Lansdale Warehouse.
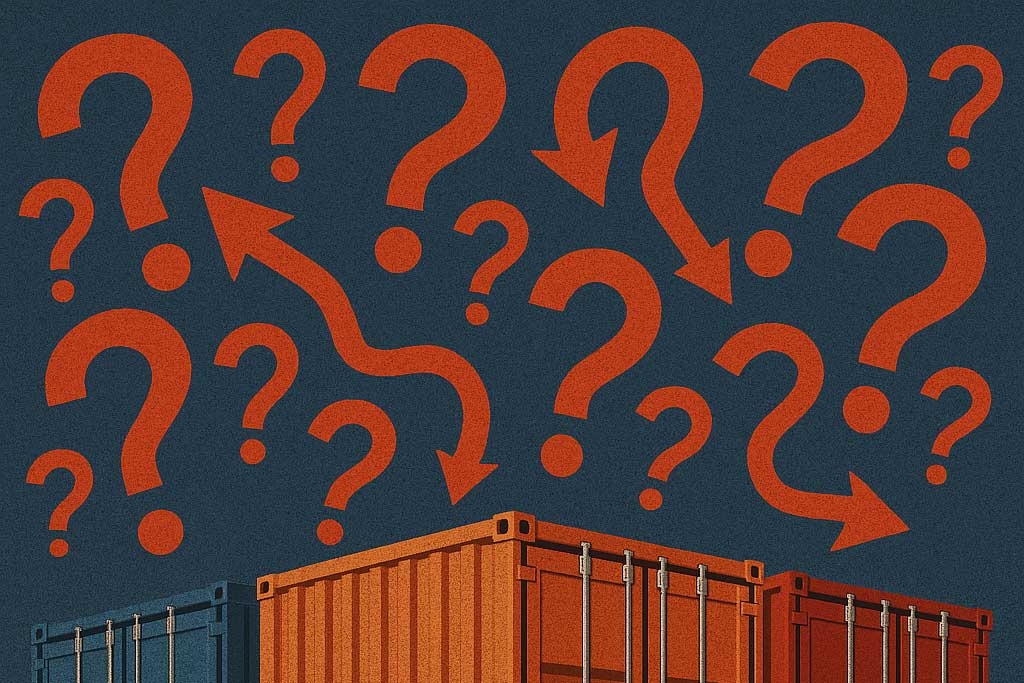
The Ripple Effect of 2025 Tariffs on Logistics
1. Shockwaves at Ports 2. Freight Costs and Supply Chain Volatility 3. Trade Diversions &[…]
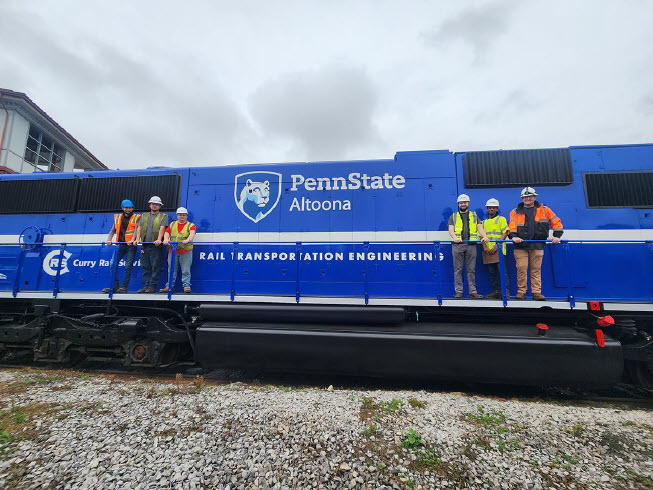
The Future of Growth in the Freight Railroad Industry
This information is the result of a Fall 2024 Penn State student project in collaboration[…]
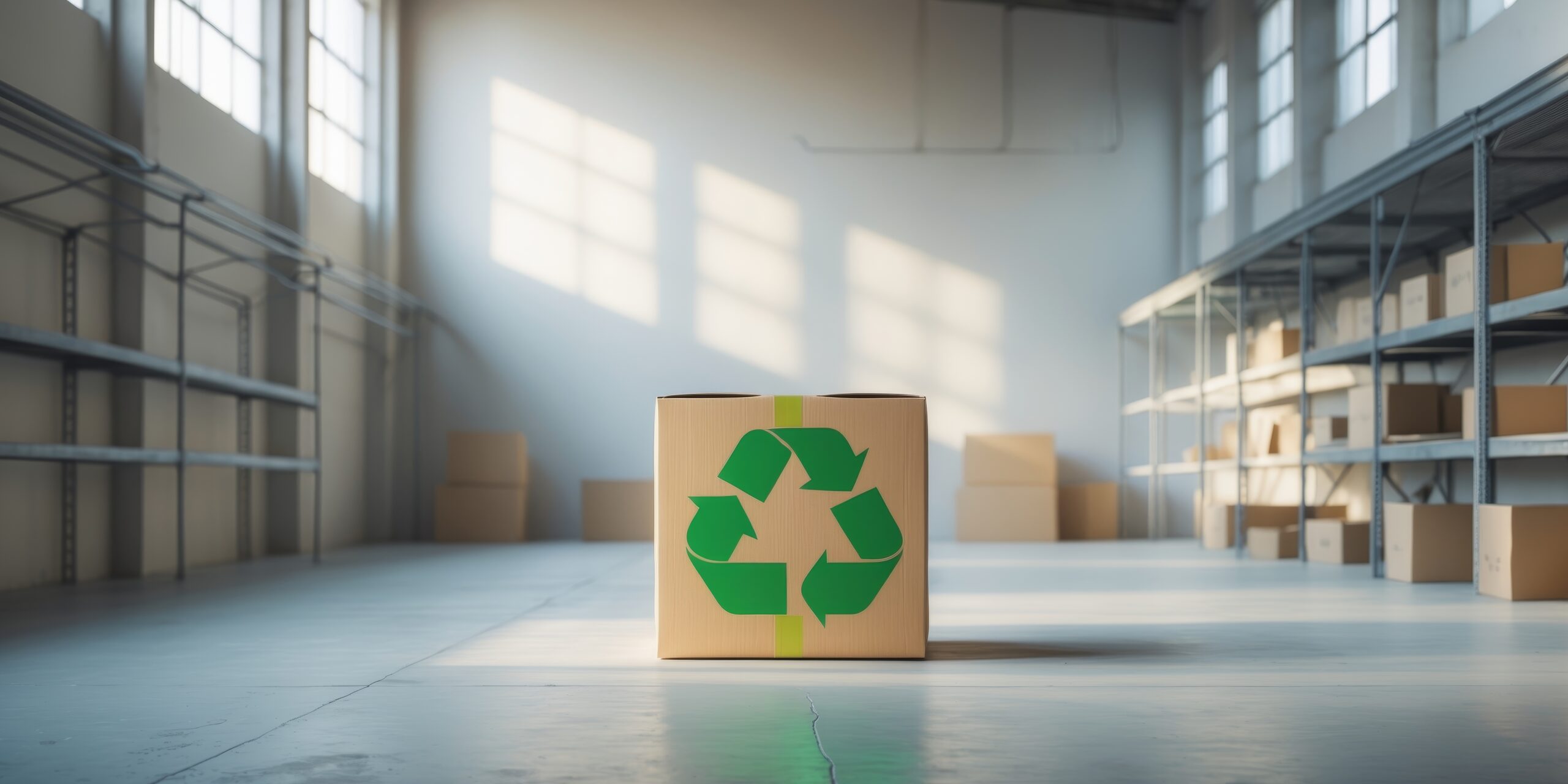
Warehouse Sustainability
At Lansdale Warehouse, we prioritize operating our business in an environmentally conscious and sustainable manner.[…]
Contact us
Got questions or ready to start a project? We’re all ears! Reach out to us today to discuss your ideas, schedule a consultation, or simply say hello. We can’t wait to hear from you!